After a promising review of my braking system design during the SAE Baja design season, the team leaders saw my potential for further involvement. They entrusted me with a crucial task: analyzing the forces within the suspension links to assist the designers. I tackled this challenge head-on with a methodical approach, First simplifying the suspension system of each corner into a quarter-car model.
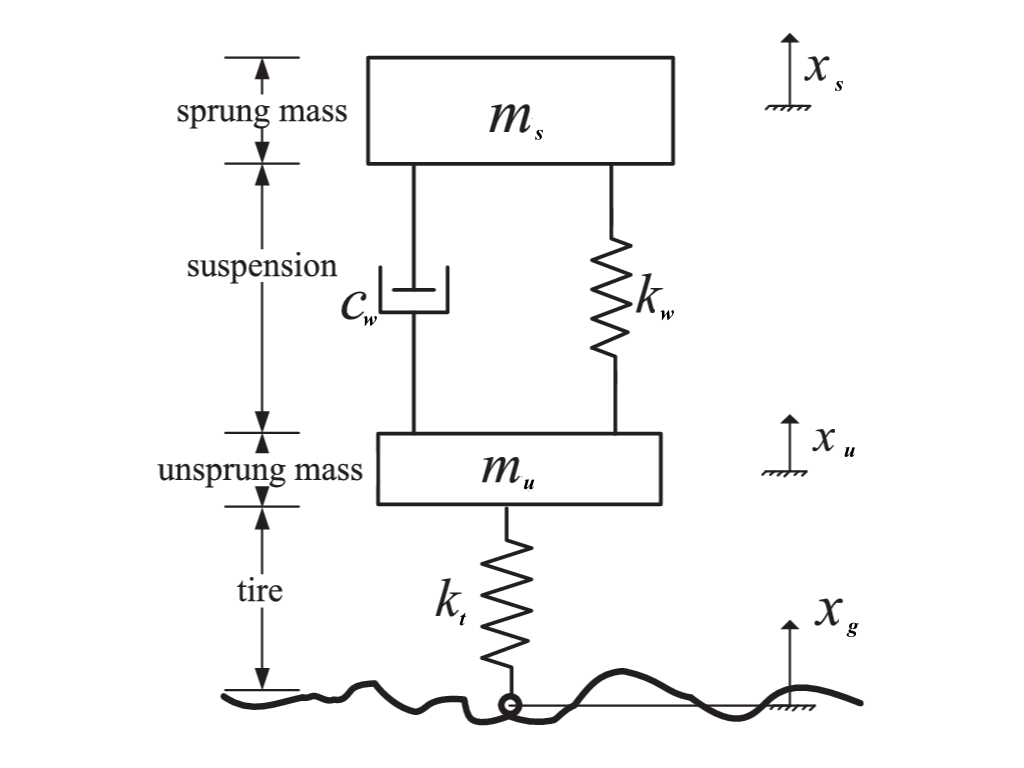
From this model, I developed a free-body diagram (FBD) and equations of motion (EOMs) for each suspension corner.
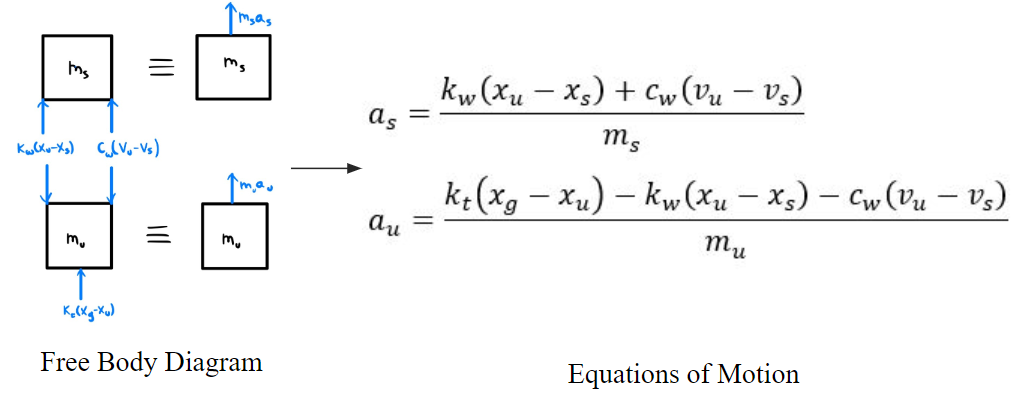
I then wrote a Python script that implemented Euler integration to solve these EOMs, determining the position of both sprung and unsprung masses at each time step. This, in conjunction with the tire’s spring rate, allowed for the calculation of forces exerted on the wheel under various bump scenarios.
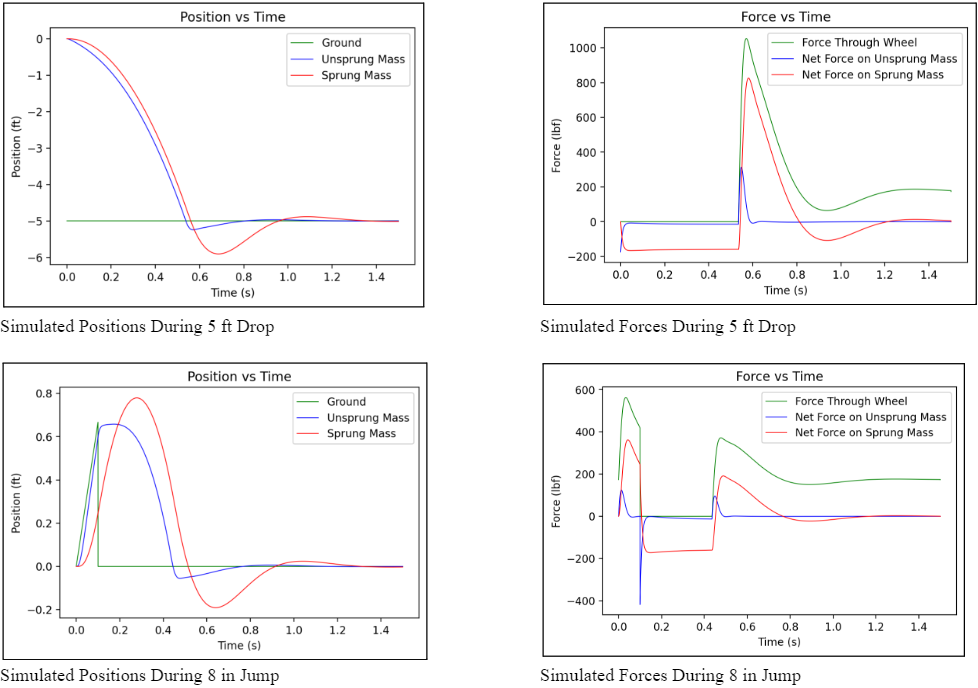
While time and budget constraints within the Baja SAE competition made physical testing of my code before vehicle design impossible, I was committed to achieving meaningful validation. To do so, I sought the expertise of Chris Bachman from Cal State, who had previously conducted similar calculations for a Baja SAE vehicle and successfully correlated them with strain gauge testing. His results demonstrated a strong agreement between calculated and measured forces on the track, providing a valuable benchmark. To establish consistency with his findings, I ran a simulation using the vehicle parameters from his research, yielding similar results. This cross-validation, even in the absence of direct physical testing, instilled confidence in the accuracy and reliability of my code.

Having established the wheel forces, the next step was to dissect their distribution through individual suspension links. To accomplish this, I employed Skyciv, a structural analysis software.

Despite its primary application in civil engineering, Skyciv’s low solve time and ease of setup for 1D beam elements made it well-suited for finding the stress distribution throughout the suspension system as a whole.
The resulting force data at each pickup point allowed the suspension designers to execute solid body FEA (Finite Element Analysis). This validated the strength of their links and informed their design decisions, ultimately contributing to the team’s success in the Baja SAE competition.