Tesla used sheet metal guards to protect the vehicle lifter belts from being punctured by bolts. One of my later tasks was to improve these guards’ design and prepare documentation to make them for all the lifters.
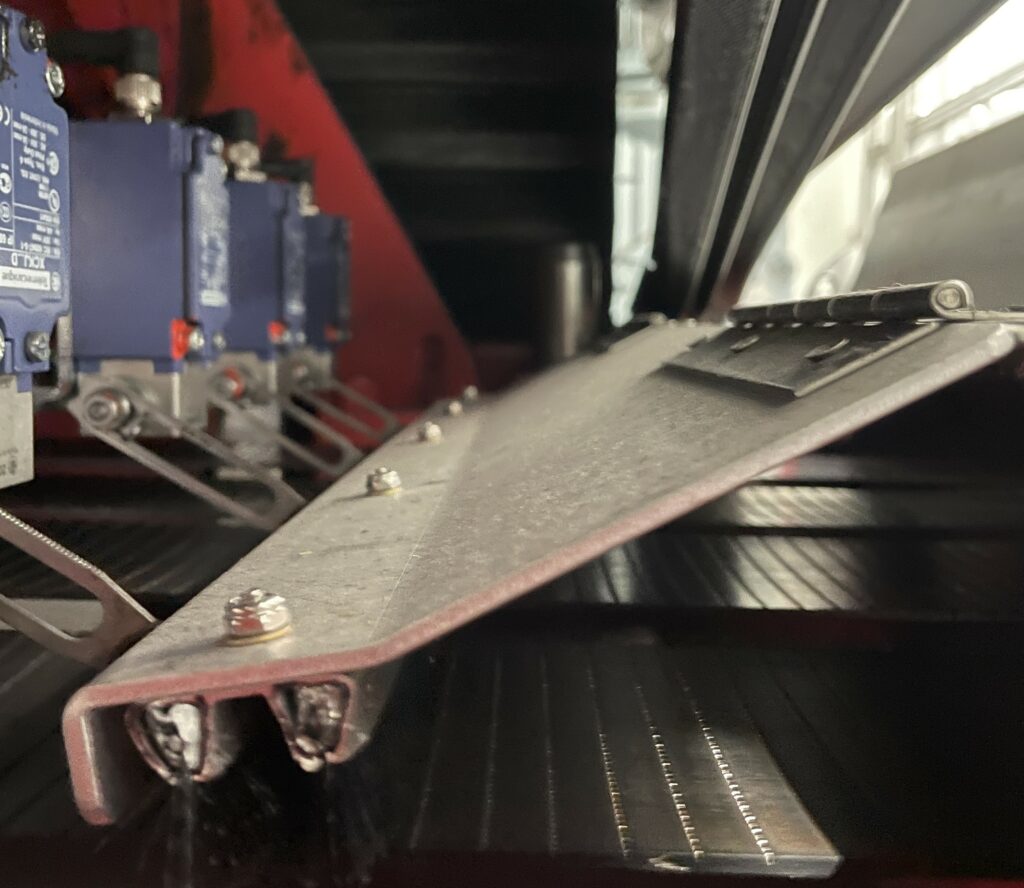
Issue | Improvements |
---|---|
Needed to be removed to grease roller bearings | Accessibility holes added to the upper structure |
Small hinge hardware was easily dropped or misplaced | less bolts used on hinges, increasing their size |
Sharp, downward leading edge caused belt wear hazard | Hemmed leading edge and increased front plate height to allow brushes to lay flat |
To implement these changes, I redesigned the part in CAD, found the necessary hardware to assemble the structure, documented everything using part drawings, and commissioned the fabrication of two sample guards from local fabricators.
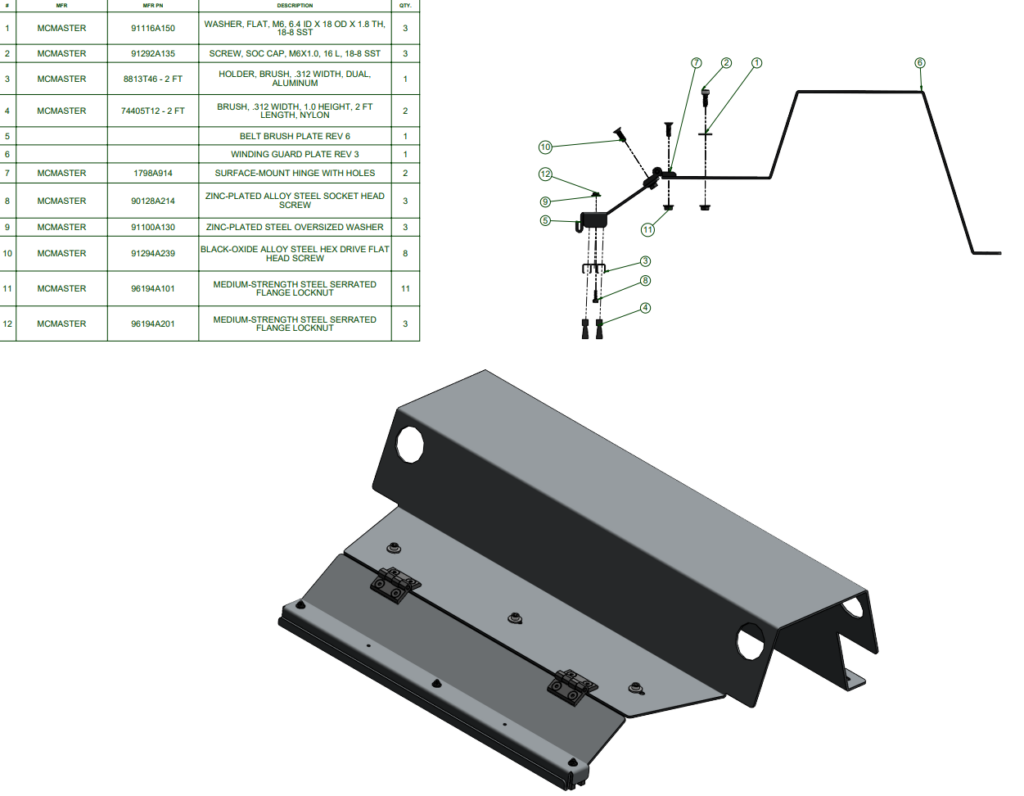
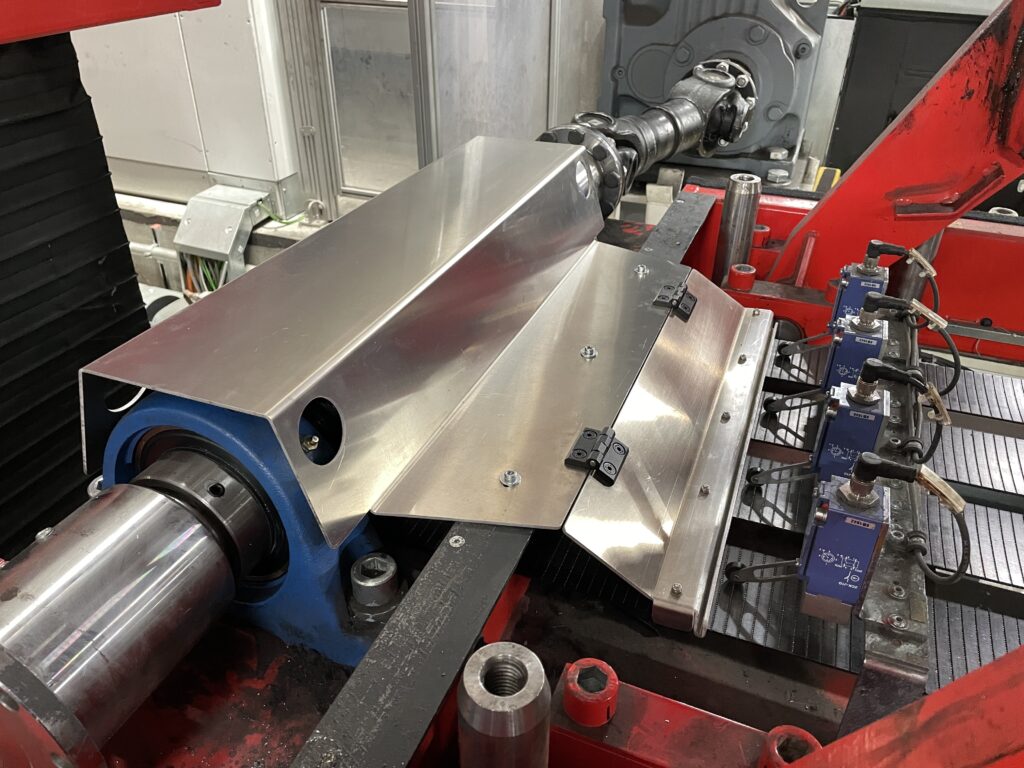
With the guard installed, I needed to test it to ensure there were no clearance issues or possibilities of excess friction flipping the leading edge back. After running the lifter through three cycles under close inspection during a shutdown, the team felt confident deploying it for production.

Despite the small clearance in the front, necessary to block the tip of chamfered bolts, this iteration of the guard saw no issues during my time at Tesla. With the documentation I created for this part, my team was prepared to order these for every lifter.