Introduction
Like many racing series, the Formula SAE competition requires safety equipment for drivers to race. I was responsible for a few safety systems on our car, specifically the impact attenuator, firewall, and head restraint.
Impact attenuator
For the impact attenuator, I had the option of making a custom device or using one of the two standard attenuators. Because a custom attenuator demands extra testing time and budget while offering nearly no performance benefit, a standard attenuator was the obvious choice.
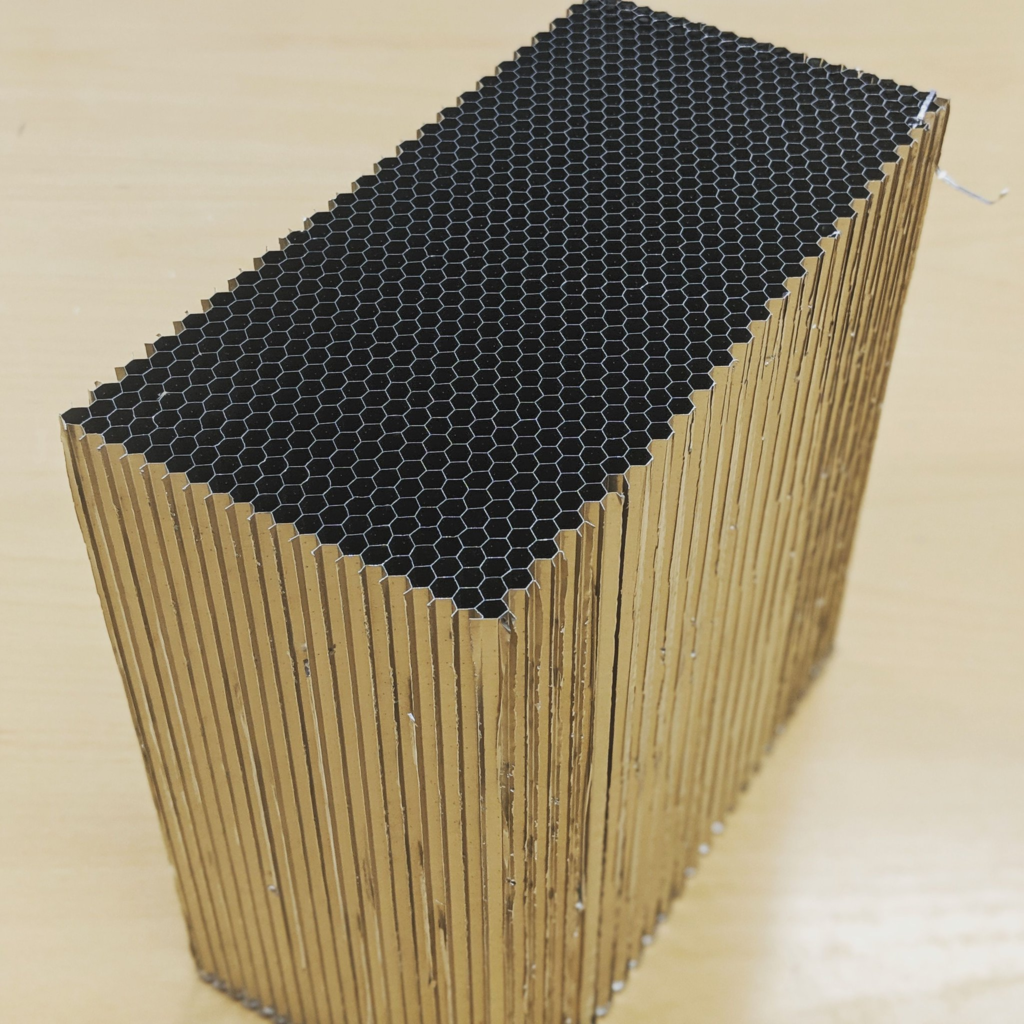
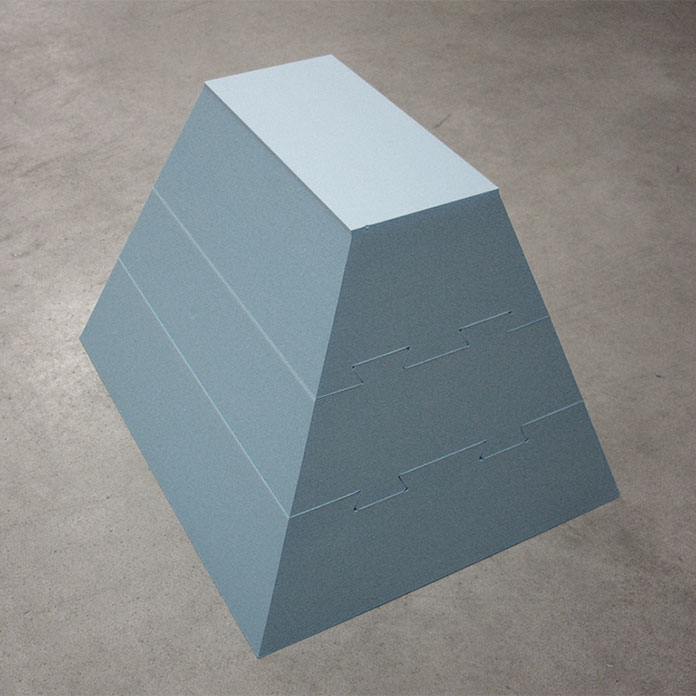
Between the two standard attenuators shown above, the honeycomb aluminum design was chosen over foam because of its smaller footprint, allowing the Aero team more space to design their nosecone.
Firewall
For the design of the structure, I utilized the Solidworks sheet metal tool, adding bends to avoid interference with the chassis. To attach the firewall, riv-nuts were used in the spots where the firewall would need to be removed and installed frequently to ease this process.
The final product was fabricated from a dual-layer system of aluminum and Nomex 410 paper.
Head Restraint
The final safety system I oversaw was the driver head restraint. It is required by rules that the mounting of this device is capable of sustaining 900N of rearward load and 300N of shear load.
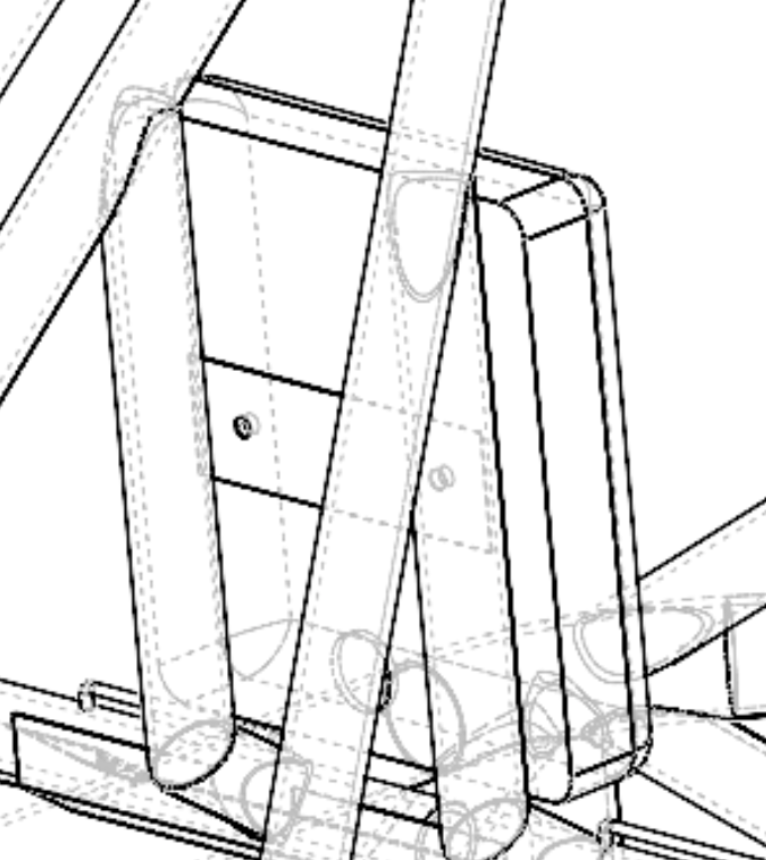
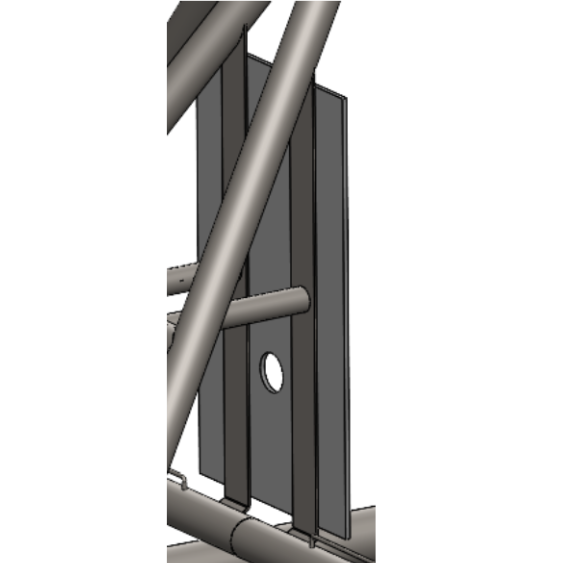
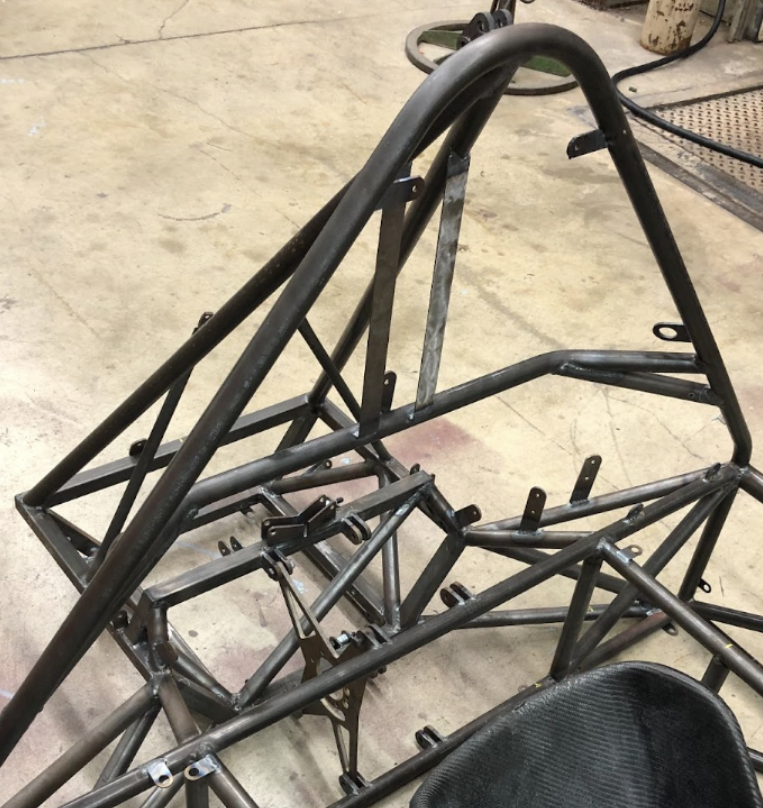
For the construction of the headrest itself, I utilized HPDE backing, Confor Impact foam, and a vinyl cover. To assemble the final product, I was able to reach out to a previous team member to do all upholstery work free of charge.
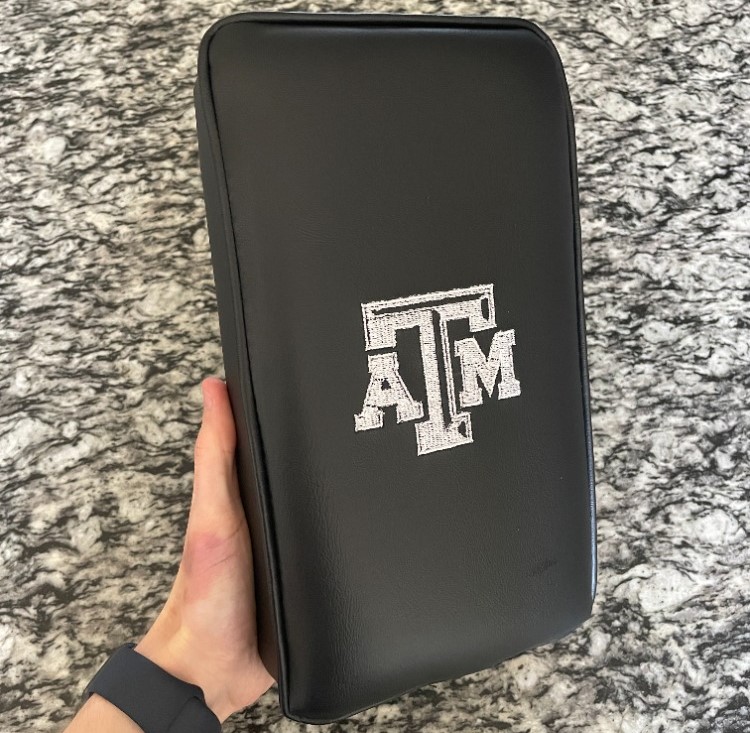
Outcome
Each system obtained approval from the inspectors, making our car the first TAMU FSAE EV to pass the rigorous tech inspection.
Learnings
While the designs were primarily rules-defined, it was an enjoyable experience to explore how to adhere to those rules while creating lightweight and user-friendly products. This is a skill I could use in industry, where many designs have to be effective while following some set of rules or codes.